GUNT DigiSkills 4
Energy efficiency in compressed air systems
Compressed air is one of the most widely used energy source in industry. There are many initiatives to make compressed air applications in companies more energy-efficient. The potential for savings is diverse and high. In addition to reducing operating costs, there is also the aspect of improving the climate situation to consider.
The topic Energy efficiency in compressed air systems of the DigiSkills 4 learning project deals with these potential savings. The didactic concept includes familiarisation with the components and learning how they work and interact. Potential savings are identified and analysed in order to achieve energy-saving operation and to create an appropriate design of compressed air systems.

1 Compressor fundamentals - Familiarisation with the components
The compressor is the central component of a compressed air system. In it, the mechanical energy supplied is converted into a pressure increase of the air.
Two typical types that work according to the positive displacement principle are the piston compressor and the screw compressor.

Augmented Reality brings the function to life. Hidden components are made visible, complex functional principles are presented in an appealing and comprehensible manner.
» Experience our example with your smartphone...
|
![]() |
2 Functional testing of compressors and compressed air systems

The functional test provides initial indications of potential savings and interactions within the system. The scope of the functional test includes work such as:
- determining pressure losses
- leak test
- measurement of volumetric flow rate, pressures, temperatures
- checking pipes
- testing the pressure switches, pressure reducers and safety valves
- checking for correct installation and adjusting the alignment
Single-stage piston compressor
with MT 142

- familiarisation with the function and testing process
- professional installation of the piston compressor including adjustment and alignment procedures
- function and operation of safety elements: pressure switch, non-return valve, safety valve
- testing and adjusting the belt tension
Two-stage piston compressor
in ET 500

- setup and function of a two-stage compressor
- measurement of relevant pressures and temperatures
- determine the intake volumetric air flow rate
- compression process on a p-V diagram
Screw compressor
in MT 175

- adjustment options on the screw compressor
- determine how long it takes to reach the final pressure
- adjust the control behaviour of the compressor
- leak test
- measurement of relevant pressures and temperatures
- determine the intake volumetric air flow rate
- oil check using a sight glass
- study continuous and short-term consumers, individually or in combination
- familiarisation with remote monitoring of the compressor unit
3 Energy analysis

The life cycle costs of a compressed air system are made up of three factors: the investment costs, the maintenance costs and the energy costs for operating the compressor.
The energy costs take up the biggest part of the overall costs. Easily realizable and usually extremely economical measures can often reduce energy costs by a third.
All components for generation, distribution, preparation and storage of compressed air need to be optimised to meet the requirements of the process. Characteristic variables such as delivery quantity, operating pressure or residual moisture are used for this purpose. With the GUNT devices MT 141, MT 142, MT 175 und ET 500, students are familiarised with the components and learn to assess errors in selection and dimensioning. Depending on the design of the compressor, the type of cooling and the operating conditions, there are three options for heat recovery: MT 175 is used to investigate the use of hot air for heating rooms. For a representative determination of demand, the compressed air consumption of the individual devices is added together and the average duty cycle is determined. MT 175 is used to analyse and compare the energy consumption of different consumers. A combination of different consumers can be studied. MT 142 und ET 500 can be used to create your own tasks on compressed air consumption. Minimising energy consumption requires the average network pressure to be adapted as accurately as possible to the effective demand. Controlling compressors allows compressed air production to be adapted to current consumption. With MT 175, the pressure level required for the respective consumer can be investigated and optimised. The maximum switch-off pressure of the compressor can be adjusted. The cycle times can be specified and the effect on energy consumption and benefits can be analysed. With ET 500 and MT 142, the switch-on pressure can be set; the switch-on times are determined by the control system. The cause of leaks is often: MT 175 can be used to analyse the effect of leaks on consumers from an energy perspective. With ET 500 and MT 142 the effects of leaks can be measured directly as pressure loss and thus in the energy consumption. Compressed air always contains impurities: However, preparation should only be carried out to the required quality in order to remain efficient. In MT 175, the compressed air is preparated with a centrifugal separator, a dryer and compressed air filters. A maintenance unit is located behind the compressed air tank. 3.1 Potential savings and realisation
Selection and dimensioning of components 20‑50%
Heat recovery 20‑50%
Compressed air demand of consumers and applications 20‑40%
Pressure head and losses 15% Controlling 20‑30%
Leaks 20‑30%
Compressed air preparation 2‑3%
MT 175 Energy efficiency in compressed air systems

Students use the MT 175 system to familiarise themselves with all the functional groups of an industrial compressed air generation system: compression, preparation, storage and consumption. Heat generated during compression is efficiently utilised to heat rooms and other spaces. The overall process is analysed from an energy perspective and potential savings are identified.
Pressure, temperature, volumetric flow rate and electrical power are measured at relevant measuring points. The GUNT software uses these to calculate characteristic variables in order to analyse the energy efficiency of the system.

Compression | Heat recovery | Preparation | Storage | Consumption | Distribution |
Intake air is filtered and compressed. Oil used for direct cooling is separated from the compressed air. | Oil heated during compression is used for space heating with the help of heat exchangers. | The impurities in the compressed air, such as oil, dust and moisture, are removed to the required quality. | A compressed air tank with safety valve and pressure gauge stores the generated compressed air. | Different consumers can be studied individually or in combination. | The pressure loss between the compressor and the consumer should be as low as possible. |
3.2 Energy optimisation and efficiencies
MT 142 with a single-stage piston compressor,
max. pressure 10bar

- energy analysis with GUNT software
- acquisition of electrical, mechanical and pneumatic power for own calculation of efficiency
- visualisation of the measured values
MT 175 as a compressed air system with screw compressor,
max. pressure 10bar

- GUNT software to analyse the energy efficiency
- acquisition of pressure, temperature, volumetric flow rate and electrical power
- calculation of characteristic variables
- analysis of energy flows within the compressed air system
- calculation of the efficiency
ET 500 with a two-stage piston compressor,
pressure 12bar

- PLC with touch screen for acquisition of pressures and temperatures in both stages as well as the electrical power consumption
- determination of intake volume flow by a nozzle on the intake vessel
- own calculation of efficiency from measured values and known performance data
GUNT Media Center
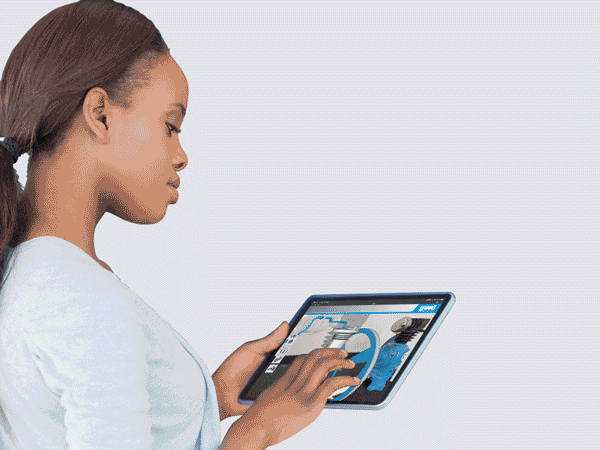
The GUNT Media Center provides a digital learning environment for all steps of the didactic concept.
- Augmented Reality interface
- extensive technical information: engineering drawings, process schematics, manufacturer documents
- videos with functional principles or assembly
- detailed manuals
- practical exercises
» further information about the GUNT Media Center
Digital media in the GUNT Media Center
Technical information

Extensive technical information clearly arranged: engineering drawings, process schematics, documents from the component manufacturers and much more.
Videos

Clear videos demonstrate the functionality of individual components, for example. Additional assembly and disassembly videos are available for the MT 141 piston compressor.
Manuals

Detailed description of the experimental unit: device setup, operation, description of the system and its software.
Digital worksheets

Assured learning success through digital worksheets. Password-protected solutions are available.
Augmented Reality

Hidden components are made visible and complex setups can be clearly demonstrated. Principles of operation are presented in an appealing manner, making the work procedure a tangible experience. Always in the context of the real environment.
Product overview
Download